1.Application:
This machine is mainly used for the production of low-carbon steel wire armor for large cross-section cables and non retreat twisting of aluminum alloy wires; It can also be used for non untwisted stranding of copper circular wire cores.
2. Main parameter:
- Low carbon steel wire:Φ1.0-Φ3.15mm
- Main stranding cage structurer: 24+24,36+36, 48+48
- Max core dia. Before armouring: ≤Φ80mm
- Rotation speed:72.5r/min(working speed)
- Armoring pitch:Stepless adjust on PLC
- Main stranding motor power:90kw (AC variable frequency motor)
- Max traction force:5 T
- Max traction line speed:30m/min
- Pneumatic caterpillar motor power:37kw (AC variable frequency motor)
- Pay-off bobbin size in cage:PN500-630
- Center Pay-off bobbin size :PN1600-PN3150
- Take-up bobbin size:PN1600-PN3150
- Machine center high:1000mm
3. Main components:
- 1600-3150mm portal pay-off rack
- Well type through wire frame
- Main cage
- Automatic side bottom loading bobbin system
- Closing wire die holder
- Non-metallic taping machine
- Metallic taping machine
- Mechanic and digital Meter counter
- caterpillar machine
- 1600-3150mm portal take-up and traverse wire rack
- Electrical control system
- Safety fence
4. Building a Rigid Type Armoring Machine: Step-by-Step Instructions
Introduction:
In this blog post, we will guide you through the process of building a rigid type armoring machine. This machine is designed to enhance the protection and durability of vehicles by applying specialized armoring materials. By following these step-by-step instructions, you'll be able to assemble your own armoring machine and potentially offer armoring services to clients in need of enhanced vehicle security.
Materials Needed:
- Steel frame and plates
- Hydraulic system (pump, hoses, and cylinders)
- Welding equipment (welder, welding rods, safety gear)
- Armoring materials (ballistic steel, bulletproof glass, Kevlar panels, etc.)
- Cutting tools (angle grinder, plasma cutter)
- Bolts, nuts, and fasteners
- Electrical components (wiring, switches, connectors)
- Control panel and gauges
- Paint and finishing materials
Step 1: Design and Planning
Before starting the construction process, it's essential to create a detailed design and plan for your armoring machine. Consider the dimensions, features, and functionality you want to incorporate. This will help ensure a smooth construction process.
Step 2: Frame Assembly
Begin by constructing the base frame using steel plates and welding them together. Ensure the frame is sturdy and capable of supporting the weight and pressure involved in armoring processes. Attach additional support beams and reinforcements as needed.
Step 3: Hydraulic System Installation
Install the hydraulic system components, including the pump, hoses, and cylinders. Follow the manufacturer's instructions for proper placement and connection. The hydraulic system will provide the necessary power for various armoring operations.
Step 4: Armoring Material Mounting
Design and fabricate mounting brackets and fixtures to securely hold the armoring materials in place. These materials can include ballistic steel plates, bulletproof glass, Kevlar panels, and other specialized armoring components. Ensure proper alignment and attachment, allowing for easy removal and replacement as required.
Step 5: Electrical Wiring and Controls
Install the electrical components, such as wiring, switches, connectors, and control panel. Follow electrical safety guidelines and consult a professional if needed. The control panel should include gauges and switches to regulate the hydraulic system and armoring processes effectively.
Step 6: Safety Precautions
Prioritize safety by incorporating necessary features like emergency stop buttons, safety guards, and warning labels. Ensure all safety mechanisms are in place and functioning correctly before proceeding.
Step 7: Testing and Calibration
Once the armoring machine is fully assembled, conduct thorough testing and calibration to ensure all components are functioning as intended. Test the hydraulic system, armoring material application, and any automated features. Make any necessary adjustments and retest until you achieve optimal performance.
Step 8: Finishing Touches
Apply a protective coating or paint to the armoring machine to enhance its durability and aesthetics. This step also helps prevent corrosion and extends the lifespan of the machine.
Conclusion:
By following these step-by-step instructions, you can successfully build your own rigid type armoring machine. Remember to prioritize safety throughout the construction process and consult professionals when needed. With your completed armoring machine, you'll be ready to provide enhanced vehicle security to clients in need.
Disclaimer: Building and operating an armoring machine requires expertise and knowledge of safety protocols. It is essential to consult professionals and adhere to local laws and regulations before engaging in such activities. This blog post is for informational purposes only and does not substitute professional advice.
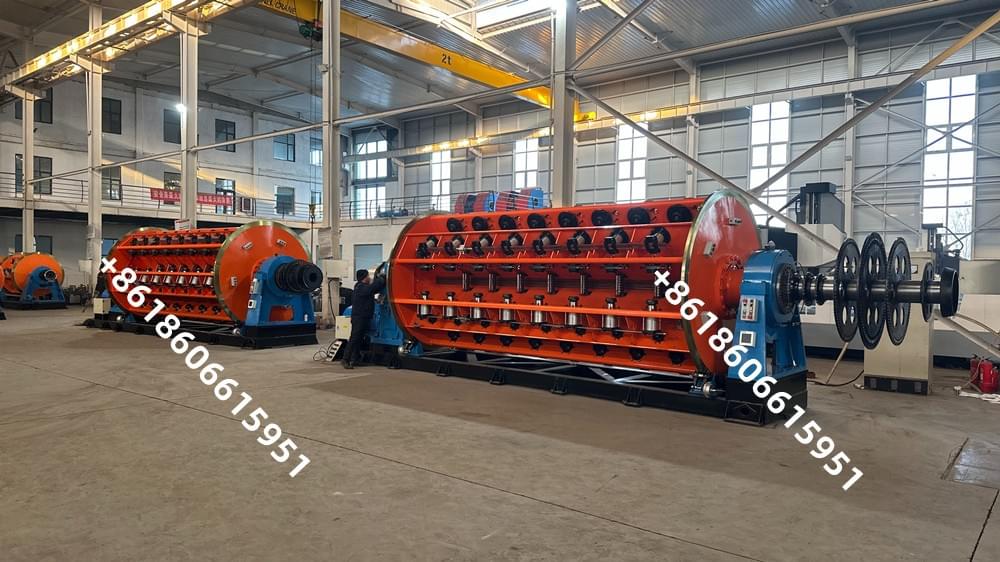
4. What are the commonly used of armoring line?
1). rigid type armouring line
2).Planetary type armouring line
3). Forky type amouring line:
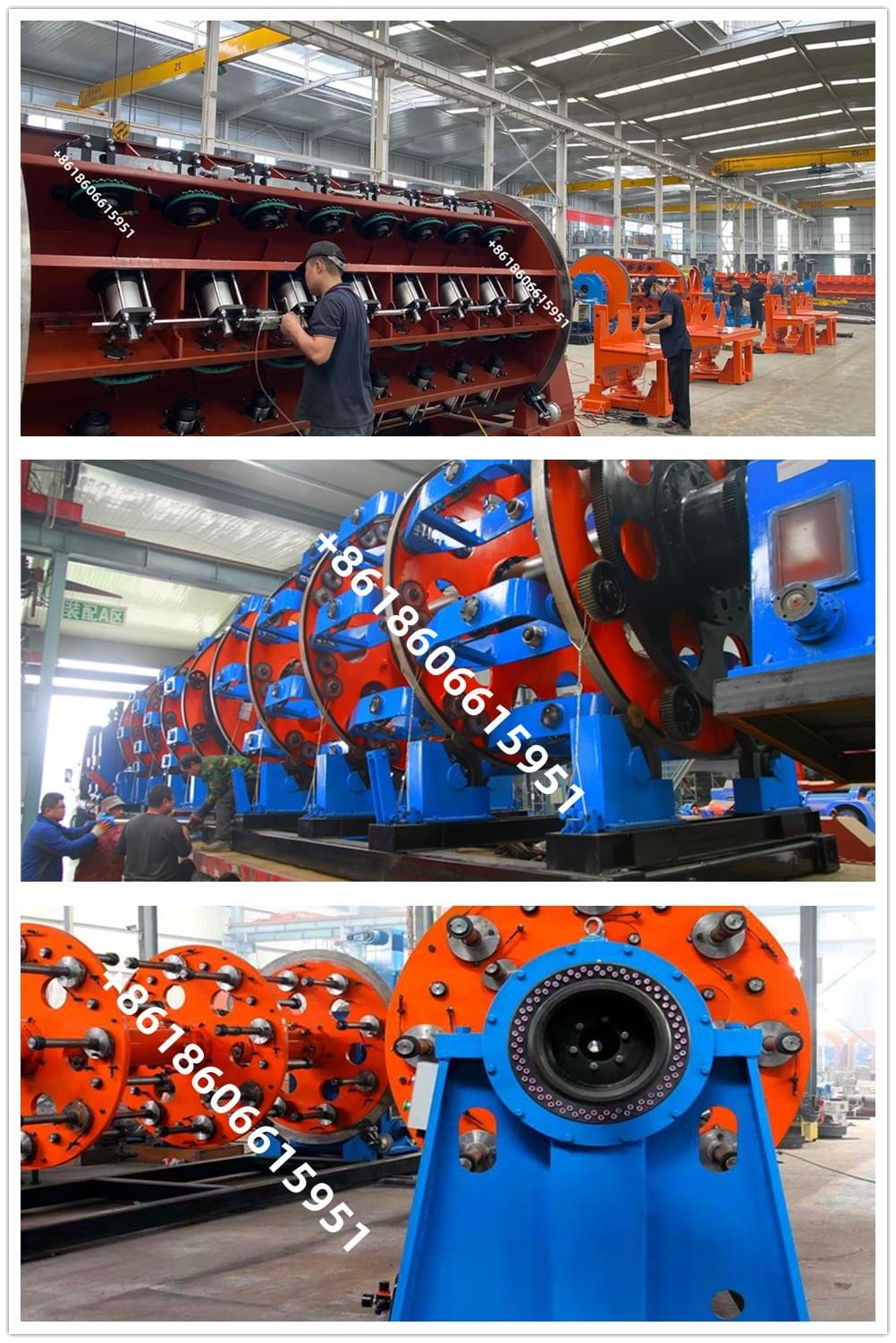
5. What different of rigid or planetary strander?
Rigid Strander:
A rigid strander is a machine used in the cable and wire industry to strand multiple wires or cables together to form a composite structure. It consists of a rotating stranding cage or drum with several bobbins or reels mounted on it. The wires or cables are fed from the bobbins and passed through a stranding die, where they are twisted together to form a stranded structure. Rigid stranders typically have a fixed stranding pitch, meaning the distance between the twists remains constant throughout the stranding process. They are commonly used for medium to large-sized cables and wires.
Planetary Strander:
A planetary strander, also known as a tubular strander or buncher, is another type of machine used for stranding wires or cables. It features a central axis or core around which multiple bobbins or reels of wires or cables are arranged. The bobbins rotate around the central axis while also rotating around their own axis. This dual rotation creates a planetary motion, hence the name "planetary strander." The wires or cables from the bobbins are twisted together as they travel along the stranding path. Planetary stranders offer the advantage of variable stranding pitch, meaning the distance between the twists can be adjusted during the stranding process. This flexibility allows for better control over the final stranded structure. Planetary stranders are commonly used for smaller-sized cables and wires.
Key Differences: BACK-TWIST
Stranding Motion: In a rigid strander, the stranding drum or cage rotates while the wires or cables are fed through a fixed stranding die. In a planetary strander, the bobbins rotate around the central axis and their own axis, creating a planetary motion.
Stranding Pitch: Rigid stranders have a fixed stranding pitch, meaning the distance between the twists remains constant. Planetary stranders allow for variable stranding pitch, enabling adjustments to the distance between the twists during the stranding process.
Application Range: Rigid stranders are typically used for medium to large-sized cables and wires, while planetary stranders are more commonly used for smaller-sized cables and wires.
Control and Flexibility: Planetary stranders offer greater control and flexibility in adjusting the stranding pitch, allowing for more precise control over the final stranded structure. Rigid stranders, on the other hand, offer simplicity and reliability in their operation but may have less flexibility in terms of pitch adjustments.
Choosing between a rigid strander and a planetary strander depends on the specific requirements of the cable or wire being stranded, such as size, flexibility, and desired control over the stranding pitch. The application, production volume, and level of customization required will also influence the selection of the appropriate stranding machine.
Real manufacturer of rigid type armoring machine:
Max Xu-China wire machinery expert
Email: cabletwister@126.com
Tel: +86-18606615951